RS485: An overview of the communication protocol
Published
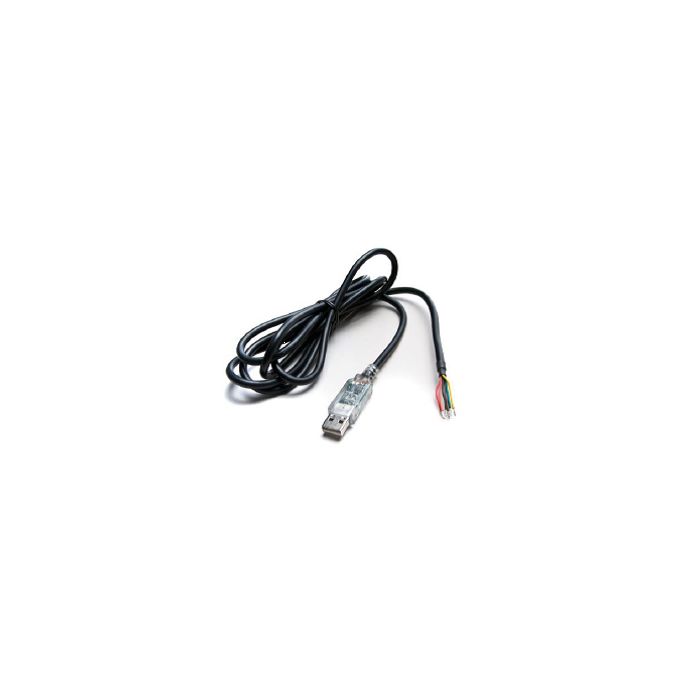
The basics of RS485
RS485, also known as TIA-485 or EIA-485, is a widely used serial digital communication protocol used in numerous industrial applications and systems. It was developed to enable the transmission of data over long distances and in harsh environments. Unlike RS232, an older communication standard designed for short distances and point-to-point connections, RS485 is capable of connecting multiple devices in a network. A key feature of RS485 is its differential signal transmission, where data is transmitted in the form of voltage differences between two wires: a positive (A) and a negative (B) conductor. This differential transmission reduces sensitivity to electromagnetic interference and enables reliable data communication over distances of up to 1.2 kilometers. RS485 supports half and full duplex communication, which means that devices can transmit and receive simultaneously. This makes RS485 ideal for systems where continuous communication between multiple devices is required, such as in industrial automation, building automation, measurement and control technology and many other applications. Communication in an RS485 network usually takes place via a master-slave architecture, where a central control device (master) sends data to and receives data from various slave devices. This makes it possible to control and monitor a large number of devices in real time. Overall, the fundamentals of RS485 provide a solid basis for the implementation of reliable and robust communication systems in industrial environments. The ability to transmit data over long distances, resistance to interference and support for multiple device connections make RS485 an essential tool in modern automation technology.
Advantages and applications of RS485
RS485 offers a number of advantages that make it a popular choice in the world of industrial communication systems. One of the most significant benefits is the ability to reliably transmit data over long distances. With differential signal transmission and support for cable lengths of up to 1.2 kilometers, RS485 allows devices to be networked over long distances without significant data loss or interference. Another important advantage is its resistance to electromagnetic interference and noise. RS485 uses differential signals in which the data is transmitted as voltage differences between conductors A and B. This minimizes the effects of interferences. This technique minimizes the effects of interference and makes RS485 particularly suitable for environments with sources of electrical interference, such as those often found in industrial production facilities. RS485 also supports multiple device connections on a network, providing the ability to connect multiple slave devices to a central master. This is particularly useful in applications where centralized control and monitoring of different devices is required, such as in building automation, monitoring systems and process control. The applications of RS485 are diverse and range from industrial automation and building automation to telecommunications and measurement technology. In industrial automation, RS485 is often used to connect sensors, actuators, controllers and other devices in order to control and monitor production processes. In building automation, RS485 enables the control of lighting systems, heating, ventilation, air conditioning (HVAC) and safety equipment. In measurement technology, RS485 is used to collect data from sensors and measuring devices and forward it to data acquisition systems. Overall, the benefits of RS485 combined with its versatility and reliability provide a robust solution for a wide range of applications where efficient and interference-free data communication over long distances is required.
Implementation of RS485 in the industry
The implementation of RS485 in industry is an essential step towards improving automation processes and increasing efficiency in various industrial applications. RS485 is widely used in industry as it provides a reliable and robust solution for data communication over long distances. The first step in implementing RS485 is to select the appropriate hardware, including RS485-enabled transceivers, sensors, actuators and controllers. These components must be properly integrated into the existing industrial network, including proper cabling and connections. Software development is another critical aspect of implementing RS485. This includes the development of communication protocols that control the transfer of data between devices, as well as the implementation of control logic that controls the processes in the plant or application. Developers can use existing libraries and frameworks to speed up implementation and reduce susceptibility to errors. The integration of RS485 into existing process automation systems is also crucial. This enables seamless communication between different components and centralized control of systems and machines. Implementation often also requires security measures to be put in place to ensure data integrity and system availability. Another important aspect of implementing RS485 in industry is the network topology. RS485 networks can be configured as bus or star networks, depending on the requirements of the application. Choosing the right topology depends on factors such as the number of devices, the distance between devices and the communication requirements. Once successfully implemented, RS485 enables reliable data communication over long distances, helping to increase productivity and minimize downtime. The implementation of RS485 in industry is therefore a crucial step towards improving automation processes and achieving efficient and reliable control and monitoring of industrial plants.
RS485 vs. RS232: Differences and comparison
RS485 and RS232 are two common serial communication standards that are used in industrial applications and many other areas, but have significant differences. One of the most fundamental differences is the signal transmission. RS485 uses differential signals, where the data is transmitted as voltage differences between two conductors, while RS232 uses unipolar signals, where the data is measured relative to ground. This differential signal transmission makes RS485 significantly more resistant to electromagnetic interference and noise and enables data transmission over greater distances, making it ideal for industrial applications. Another difference concerns the number of connected devices. RS485 supports multiple device connections in a network, which means that several devices can be connected together in a bus or star network, while RS232 usually allows point-to-point connections between two devices. This makes RS485 particularly suitable for applications where a large number of devices need to communicate with each other, such as in industrial automation. The voltage levels are another difference. RS232 uses higher voltage levels (+12V to -12V), while RS485 uses lower voltage levels (+5V to -5V). This difference can have an impact on the power supply and signal level adjustment. In terms of cabling, RS485 usually uses twisted pair cables, while RS232 often uses simple single core cables. This choice of cable types can affect installation costs and susceptibility to interference. Overall, both RS485 and RS232 offer specific advantages and are suitable for different applications. However, RS485 shines in industrial environments where reliable data communication over long distances and between many devices is required, while RS232 is used in less demanding applications.