CNC programming - Everything you need to know
Published
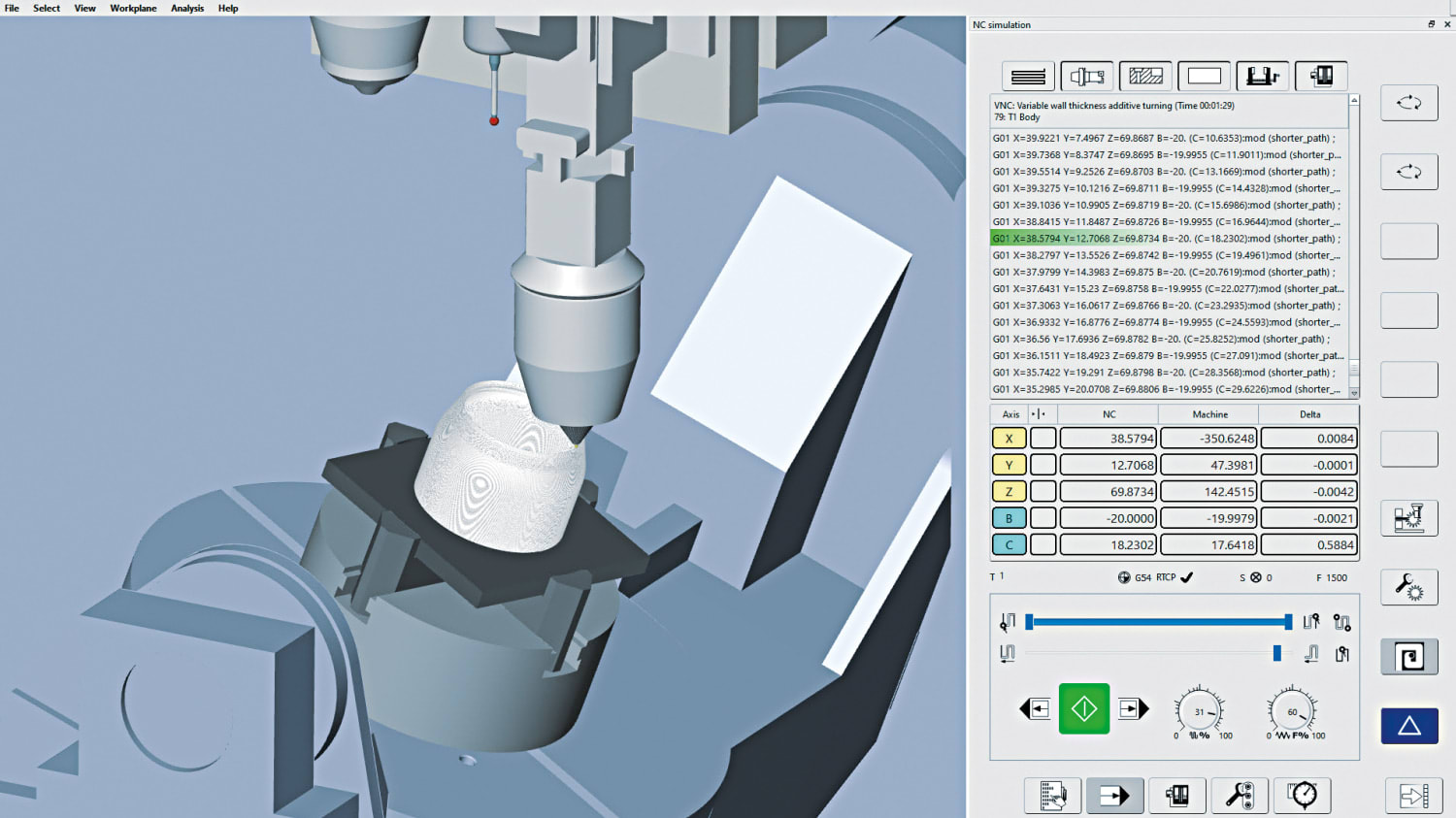
CNC stands for "Computer Numerical Control". CNC programming refers to the process of creating instructions or codes that are generated by a computer. interpreted are used to precisely control and regulate machine tools such as milling machines, lathes or laser cutting machines.
Instead of manually issuing commands to the machine, CNC programming creates specific instructions in the form of numerical code that defines the movements of the machine, the positioning of tools and other machining operations. These instructions are often written in a special CNC programming language based on G-code or a similar standardized format.
CNC programming offers several advantages:
- Precision: CNC machines can carry out high-precision work because they respond to precise numerical instructions.
- Repeatability: Once a CNC program has been created, it can be used again and again to manufacture identical parts or products.
- Complexity: CNC programming can be used to automate complex machining processes that would be too difficult or time-consuming for manual operation.
- Efficiency: CNC machines can work around the clock, which increases production capacity.
CNC programming requires knowledge in interpreting technical drawings, creating G-code or similar command structures, selecting the right tools and cutting parameters, and considering safety aspects. CNC programming is used in many manufacturing industries, from automotive to aerospace, electronics manufacturing, medical technology and more.
What are the prerequisites for mastering CNC programming?
Mastering CNC programming requires a combination of technical knowledge, practical experience and problem-solving skills. Here are some key requirements needed to be successful in CNC programming:
- Basic technical knowledge: An understanding of mechanical engineering, mechanics, mathematics (especially trigonometry) and geometry is essential to understand the operation of CNC machines.
- Technical drawings: The ability to read and interpret technical drawings is essential to understand what machining operations need to be carried out on a workpiece.
- CNC technology: A basic understanding of how CNC machines work, including their axes, tool changes, clamping systems and tool holders, is required.
- Knowledge of materials: Understanding the different materials and their processing properties is important to determine the correct cutting parameters.
- Programming languages: Experience with CNC programming languages such as G-Code or ISO 6983 is necessary to create accurate and efficient programs.
- CAD/CAM software: The ability to use computer-aided design (CAD) and computer-aided manufacturing (CAM) software to model workpieces and generate CNC programs is critical.
- Practical experience: The actual programming and operation of CNC machines requires practical experience in order to put theory into practice.
- Problem solving skills: CNC programming often involves identifying and solving problems, whether related to tool selection, cutting speeds or other aspects.
- Safety Awareness: A thorough understanding of safety guidelines and procedures when working with CNC machines is essential to avoid injury and damage.
- Willingness to learn: CNC technology is constantly evolving. Therefore, the willingness to continuously learn about new technologies, tools and methods is important in order to stay up to date.
- Attention to detail: The ability to create precise and accurate programs is crucial to producing quality products.
Mastering CNC programming requires time, commitment and hands-on practice. This can be achieved through training, courses, professional experience and working on real projects.
What else should you know about CNC programming?
Here are some additional important information and aspects to know about CNC programming:
- Different types of CNC machines: There are different types of CNC machines, including CNC milling machines, CNC lathes, CNC laser cutting machines, CNC waterjet cutting machines and more. Each type of machine has specific applications and requires customized Programming .
- Material processing: CNC machines can process a wide range of materials, including metals, plastics, wood, ceramics and more. The choice of the right cutting tools, cutting parameters and cooling methods depends on the material to be processed.
- Tool change and tool paths: Programming involves selecting the right tools and defining the tool paths that guide the tool through the workpiece. Efficient tool changes and a smart choice of paths can significantly reduce machining time.
- Simulation and verification: Before a CNC program is executed on an actual machine, it is advisable to check it using simulations and verification software. This allows errors to be detected and expensive mistakes to be avoided.
- Program optimization: Experienced CNC programmers can optimize programs to shorten machining times, reduce tool wear and improve surface quality.
- Postprocessor: A postprocessor is software that converts the CNC program generated by the CAM system into a specific machine code (G-code or similar) that the machine can interpret.
- CNC in Industry 4.0: Modern manufacturing processes often integrate CNC technology into the concept of Industry 4.0, in which CNC machines are networked with other systems and data sources to enable automated and efficient production.
- Advanced machining strategies: In addition to basic cutting operations, there are also advanced strategies such as 5-axis machining, high-speed machining, adaptive roughing and more that can increase the efficiency and quality of CNC machining.
- CNC programming for prototypes and small series: CNC technology makes it possible to produce prototypes and small series economically without having to use expensive tools for mass production.
- Career opportunities: CNC programmers work in a variety of industries, including manufacturing, automotive, aerospace, medical and electronics manufacturing. These positions require specialized skills and offer good career opportunities.
CNC programming is a multifaceted field that requires continuous training to keep up with the latest developments in technology and to offer high-quality machining solutions.
Who is CNC programming not suitable for?
CNC programming requires specific skills and interests. There are certain characteristics and circumstances where CNC programming may not be a good fit:
- Lack of interest in technology and machines: If someone has no interest in mechanical engineering, technology or mechanical processes, CNC programming may be less appealing.
- Limited math and geometry skills: CNC programming requires basic knowledge of math and geometry, especially trigonometry. Individuals who have difficulty with these concepts may feel uncomfortable with programming.
- Impatience: CNC programming often requires patience and precision. Quick solutions may not always be the best, as errors must be avoided.
- Lack of willingness to undergo continuous further training: The CNC Technology is constantly evolving. If you are not prepared to keep up to date with new technologies, methods and tools, you may find it difficult to stay up to date.
- Fear of technology: If someone has a fundamental fear of technology or computers, CNC programming could be challenging as it requires working closely with computer-controlled machines.
- Physical limitations: The operation and maintenance of CNC machines may require physical exertion. Persons with severe physical limitations may have difficulty performing these tasks.
- Short-term projects or small quantities: If someone is mainly interested in short-term projects or producing very small quantities, setting up and programming CNC machines might be too time-consuming.
- Aversion to detail work: CNC programming often requires careful detail work to create accurate programs and avoid potential errors. People who find this difficult may become frustrated in this environment.
- Lack of understanding of technical drawings: If someone has difficulty interpreting or understanding technical drawings, it could be challenging to understand the requirements for machining.
- Little interest in crafts and manufacturing: CNC Programming is often closely linked to manual skills and production processes. People who have no interest in these areas may find it difficult to get to grips with CNC programming.
It's important to recognize that while CNC programming requires specialized skills, it can also be a highly rewarding career for those with the necessary qualifications and interests.