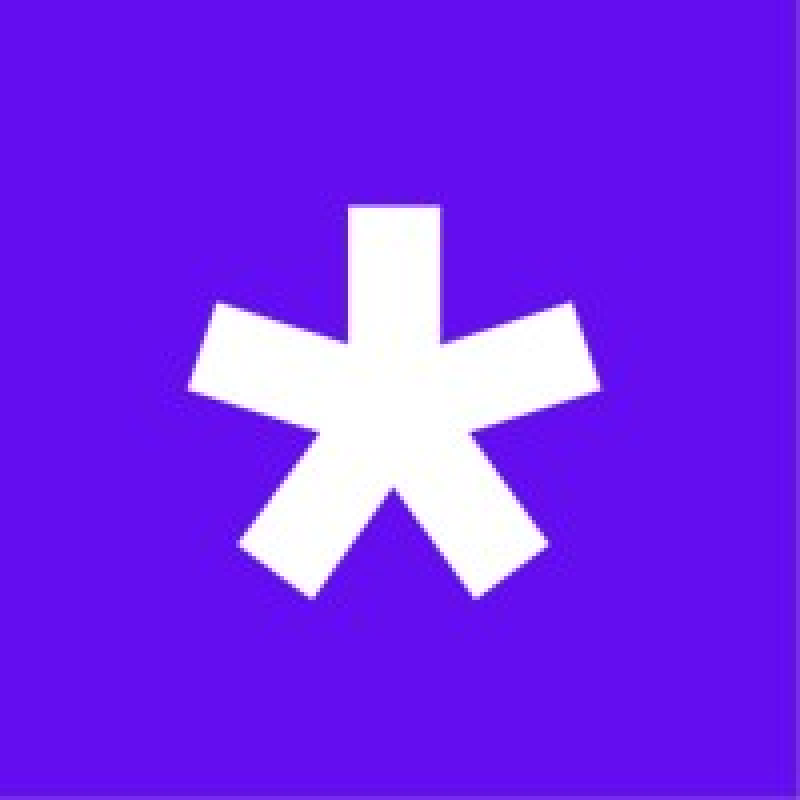
Exponent – Meistere deine Tech-Interviews mit Probegesprächen und Experten-Coaches von Top-Unternehmen.
Gesponsert von ExponentBy clicking the “Apply” button, I understand that my employment application process with Takeda will commence and that the information I provide in my application will be processed in line with Takeda’s Privacy Notice and Terms of Use. I further attest that all information I submit in my employment application is true to the best of my knowledge.
Job Description
OBJECTIVES/PURPOSE
The Automation engineer II is integrated in the automation structure.
Background:
Automation Engineering is the core foundation for OT Shopfloor Systems & Data Access and as such a key element to introduce Industry 4.0 to provide shopfloor data for data science & analytics on industrial scale.
The target of Automation Engineering is that all manufacturing systems are following an end-to-end harmonized way to utilize shopfloor data from a seamlessly integrated & modernized and secure automation system landscape. Shopfloor integration follows an automation standard framework, the automation obsolescence is managed risk-based including cybersecurity & data integrity mitigations and a game-changing speed up of shopfloor data availability & utilization per site materializes.
The manufacturing site of Lessines is composed of purification, filling and packaging lines. Its activities is supported by utilities systems such as a power plant area.
The installation, programmation, configuration and support of those equipment are managed by the automation team.
The automation system consists of Osi-Pi, MES, supervision systems, DCS, PLCs/Panels, UPI systems (Systech), Oracle and SQL databases, drives...
The automation team is split in three area: support, project and strategy.
Depending of the area the scope position is to:
- Be the Technical system support (troubleshooting, improvement) and automation SME to support and implement process, data driven or innovative solution;
- design, installation/modification, commissioning and qualification of automation systems according to EHS, GMP (Good Manufacturing Practices) and GEP (Good Engineering Practices) requirements;
- continuously improve automation process and standard
SCOPE
Financial:
Up to 500k
Leadership/People:
No. Of direct report: up to 3 external partner
Geographic Scope:
Local (Belgium Lessines) – No travel requirements
*if applicable
ACCOUNTABILITIES (Describe the primary duties and responsibilities of the job. Include only the essential functions of the job. Approximately 5 – 10 bulleted task statements should be identified).
The incumbent must be able to manage, without assistance, automation modifications or be integrated in larger projects teams. In particular, the position implies :
Support:
- Technical system support (level 2) for automation, MES and UPI (Systech)
- Reduce automation issues on existing systems (improvement)
- Support investigation by providing automation expertise
- Developp and implement complexe change on automation, MES and UPI systems (Systech)
- Provide support for the deployment of use case for data, innovation and for AIMP
Projects:
- Prepare future manufacturing project (pre-capex) including:
technical study (internalized or externalized)
Provide automation standard / tender
Project plan preparation (including offer from automation/ engineering partner)
- Follow manufacturing project (capex) including:
provide automation expertise
Partner follow up (technical and documentation)
participation in the project execution and implementation
Strategic activities
- participate in the creation of automation standard
- Work with global automation and local IT to deploy Global automation program and ensure standard approach on all project
- Analyse and Improve the efficiency of the team during change control activities
- Create and deploy automation obsolescence program
Common activities:
- Provide 24/24 7/7 off-site support (level 2)
- Coordonate technically up to 3 automation engineers
DIMENSIONS AND ASPECTS
Technical/Functional (Line) Expertise (Breadth and depth of knowledge, application and complexity of technical knowledge)
Able to understand technical installations, equipments and sytems used on the site. Able to be a technical leader inside project development, investigations and routine problematics. Comfortable with technical & quality documentation according to GxP.
Leadership (Vision, strategy and business alignment, people management, communication, influencing others, managing change)
Consistently exhibits Leadership Behaviors (Be Positive, Result-Driven, Accountable and excellent manager of himself and others) in the execution of activities, and encourages others to do the same.
Develop his or her leadership sensitivity a multidisciplinary team. (Act as a technical leader).
Able to coordinate technical activities of up to 3 automation engineers.
Decision-making and Autonomy (The capacity and authority to make organizational decisions, autonomy in decision-making, complexity of decisions, impact of decisions, problem-solving)
Able to be factual to report problematics and propose “ready to decide” solutions on complex issues. Able to quick fix any operational issues during 24/7 service.
Interaction (The span and nature of one’s engagement with others when performing one’s job, internal and external relationships)
Collaborative and proactive member inside a multi-disciplinary team. Able to interact with other departments with demonstrated communication skills.
Innovation (The required level of scientific knowledge, knowledge sharing, innovation and risk taking)
Participate to benchmark and innovative ideas, proposes new design concepts.
Complexity (Products managed, mix of businesses, internal and/or external business environment, cultural considerations)
Deploy Takeda EHS culture by applying security rules and giving regular positive and constructive feedback on initiatives that insure/improve the safety of the employees on the work floor.
He or She is aware of the complexity of products manufactured by TAKEDA Lessines, the complexity of pharmaceutical sector. He or She is also able to understand humans challenge complexity, to be able to respect any interlocutors by applying TAKEDA ethics code.
EDUCATION, BEHAVIOURAL COMPETENCIES AND SKILLS: (List the essential and desirable education and competency requirements to perform the primary responsibilities of the job. Any minimum requirements should be noted.)
Education / experience:
- Master degree in Automation, Electrics: (Or Bachelor degree+ Exp.)” with at least 5 years’ experience in automation pharmaceutical domain.
- Comfortable with the technology evolution for automation systems.
Core Competencies / Skills / Leadership Behaviors:
- Good communication skills and the ability to lead and perform effectively in multi-disciplinary teams
- Must have the ability to effectively participate to Engineering projects, coordinate suppliers, and drive results.
- Has the ability to prioritize multiple tasks and work on multiple projects simultaneously.
- Develop his (or her) understandnis of business drivers and customer needs.
- GAMP5 Methodology
- Experience with Quality Systems and Processes in a GMP regulated and FDA+Eudralex licensed manufacturing site.
- Must have good experience in project management, preparing project budgets and timelines
- Must be comfortable with MS OFFICE Pack (Especially WORD, POWERPOINT, EXCEL).
- Must be sensitive to Data Integrity aspects.